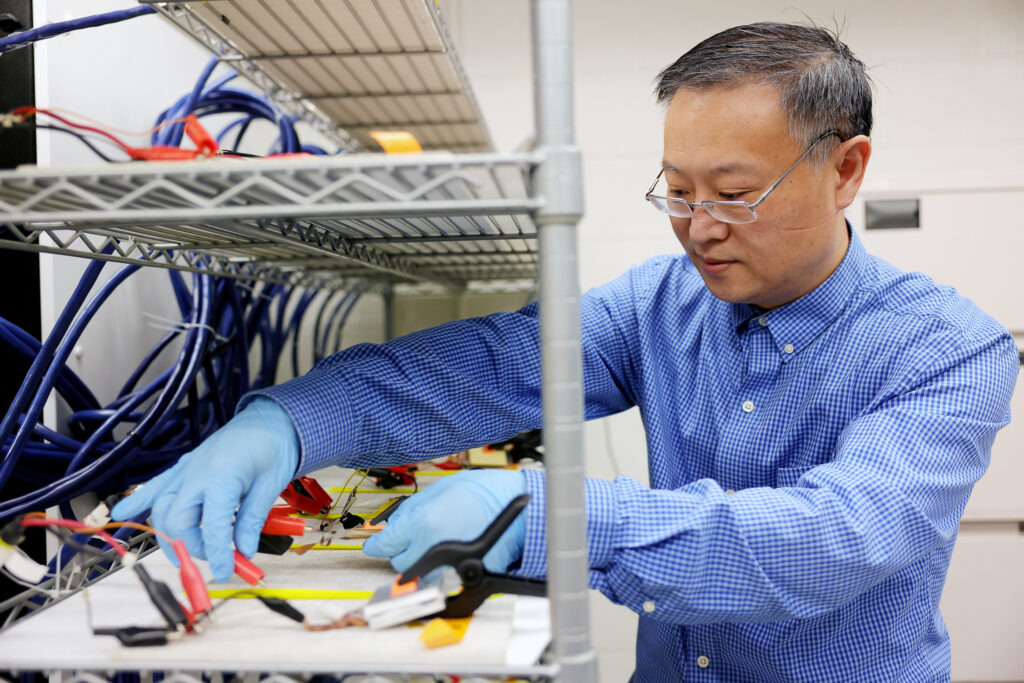
Mechanical engineers at the University of Michigan (U-M) are developing an approach that integrates physics-based modeling and machine learning to rapidly and accurately determine the state of health and remaining useful life of battery cells.
The project is funded by an Advanced Research Projects Agency-Energy (ARPA-E) award totaling nearly $3 million and is led by Wei Lu, professor of mechanical engineering.
The growth of electric vehicle manufacturing in recent years has increased demand for technologies that optimize production, lower consumer costs, and promote sustainable practices. The U-M-led project aims to address these needs by significantly reducing the time it takes to assess the state of health of electric vehicle batteries.
Electric vehicles rely on electric motors and battery systems. Monitoring the battery’s state of health is comparable to tracking mileage in a gasoline-powered car—but it is even more critical.
As batteries in electric vehicles age, their capacities decrease. Rapidly assessing a battery’s state of health is essential for maintaining the performance and reliability of electric vehicles, while employing control strategies to prolong battery life, Lu explained. The battery in an electric vehicle accounts for approximately one-third to one-half of its cost.
Traditionally, battery capacity is measured by fully charging the battery and then discharging it at a very slow rate, which can take up to 10 hours or more for a single battery.
The U-M project introduces an innovative solution by integrating physics-based modeling and machine-learning techniques. This approach enables rapid determination of battery health and remaining useful life, marking a significant advancement in battery management technology, Lu explained.
“Machine learning is good at interpolation,” Lu said. “It’s only as good as the data it has seen. Physics-based modeling is very good at extrapolation.”
A pure machine-learning approach relies on large amounts of training data, but obtaining labeled battery data is often time-consuming, costly, and sometimes impractical.
When battery chemistry is changed or a new batch of batteries is encountered, the machine-learning model must be retrained, adding to the challenge. This approach is also hindered by cell-to-cell variations—even within the same batch, individual battery cells will demonstrate differences from one another—which machine learning cannot capture.
For rapid state of health estimation, battery cells can only undergo shallow charge and discharge due to limited time. As a result, the resulting data lack deep cycling information, preventing their use for training machine learning algorithms in capacity prediction.
Lu’s innovation lies in integrating machine learning and physics-based modeling, enabling in-depth analysis of battery states—including capacity, state-of-health, and other internal battery states—using only shallow charge and discharge data.
“Currently, when people talk about state of health, they are primarily talking about capacity or resistance,” Lu said. “But we know more. With the physics-based model, we can actually tell what happens inside the battery from the model—the thickness of the solid electrolyte interphase, active material state of charge, loss of anode and cathode materials—all these internal states can be determined from the physics-based model.”
A reduction in the time it takes to determine the state of health and remaining useful life of battery cells would offer more than convenience—it would be critical for real-time battery management in electric vehicles to optimize battery performance and ensure safe and efficient operation. It also enables improved manufacturing practices and informed strategies for reuse, recycling, and repurposing after their removal from vehicles.
Manufacturers don’t currently have a tool to quickly and accurately estimate the capacity of batteries and therefore tend to overcompensate for possible capacity loss over time. This tendency increases the cost of vehicles and waste involved in the manufacturing process, Lu explained.

Rapid determination of battery health would lead manufacturers to better understand the required capacities of electric vehicle batteries, helping to avoid price hikes and reduce waste.
The ability to swiftly determine a battery’s state of health and remaining useful life can revolutionize how batteries are repurposed once they fall below optimal capacity for electric vehicles. Batteries can be repurposed for stationary use, regenerated for reuse, or pared down for materials, all depending on their remaining utility.
“For many car manufacturers, once it’s reduced to 80% state of health, the battery will be removed from the car for second use,” Lu said. “If you do recycling, you want to know what the residual value of the battery is, and it’s not practical to take 10 hours to determine the capacity. You want to know very quickly.”
Rapid, real-time state of health assessment will also help inform the development of strategies to prolong the life of vehicle batteries. This technology enables the vehicle’s on-board battery management system to protect and avoid stressing the battery, ultimately making it last longer—another benefit to both consumers and the environment.
U-M Mechanical Engineering students and postdoctoral fellows will also have opportunities to participate in Lu’s research, gaining valuable experience that aligns with the rapid advancements in the energy and electric vehicle industries.
This battery management technology exemplifies how integrating machine learning and physics-based modeling can fuel technological breakthroughs and industry advancements.
“Thinking outside of the box can help generate innovative solutions to help shape the future of the energy sector,” Lu said.